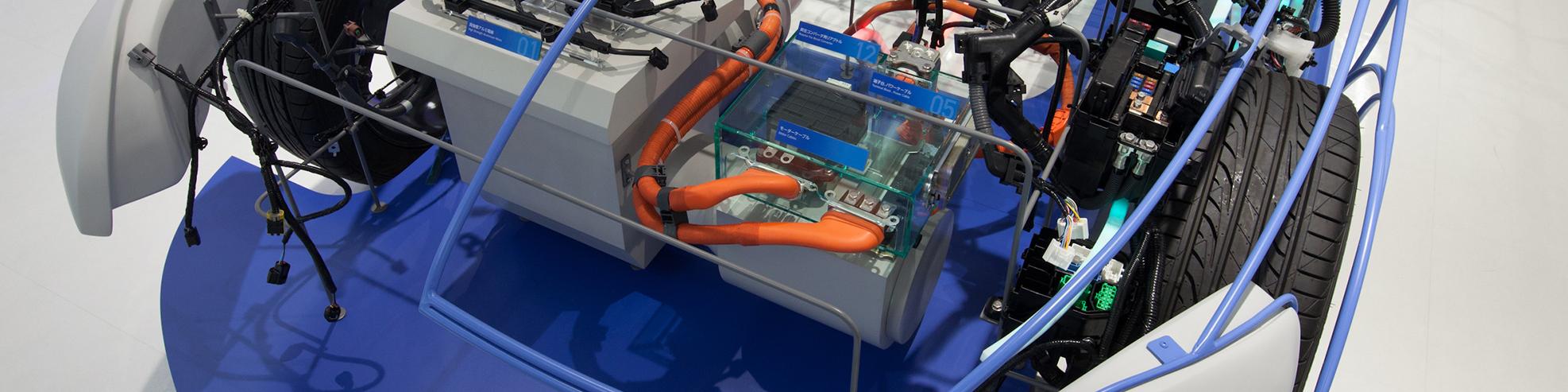
In order to ensure the reliability of the aluminium wire bundle ~ strength and conductivity to ensure ~
The development of new aluminum alloy
Compared to aluminum and copper, low conductivity, to achieve the same resistance, it must increase wire cross-sectional area.After wire cross-sectional area increase, lightweight effect will be reduced accordingly.Otsuka et al., this paper discusses the displacement with the physical properties of materials: past copper wire size is generally low voltage wires used was 0.5 (wire cross-sectional area), and aluminum wire is within 0.75 was able to control the size.Only need to add elements, conform to the purpose of get want new aluminium alloy.Subsequently, and sumitomo electric and electronic materials research institute of energy after repeatedly to discuss, we reached the conclusion that to inhibit electrical conductivity decreased at the same time, enhance strength, effective means is to add Fe (iron).
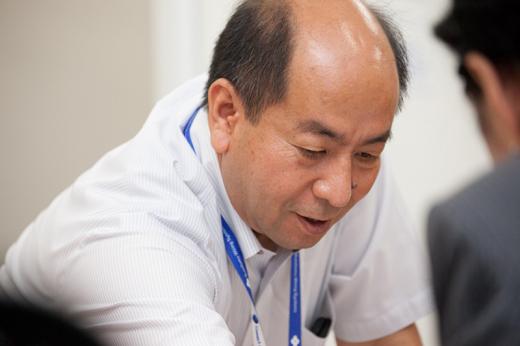
And, on the other hand, the development of a new aluminum alloy is the production of the discussion."Aluminium and copper compared to the same cross-sectional area under the lower intensity.Implementation of material in the lab, can actually production in the factory?The wire要经过拉丝、绞合、压制等制造工序,但最让人担心的就是断线。我们致力于在各个工序中降低拉力和摩擦,以建立与铜线生产同等水准的高生产性为目标”(住友电装电线事业本部技师长·冈本治)。
"Wire conductor using bare wire (aluminum) phi is 0.15 ~ 0.4 mm, very thin, we found that as Fe (iron), with the increase of adding amount of wire drawing and stranding the processability of would be reduced.So we started on the premise of not impede processability, looking for replacement parts of Fe (iron), enhance the strength of the second add elements "otsuka (the above).Otsuka et al. review in widens the relationship between strength and conductivity, judge can allow conductivity decreased to some extent.So in comparison to explore various elements, we found that Mg (magnesium) is the most suitable.Aluminum (Al), Fe (iron), Mg (magnesium) optimization combination, can well meet the requirements of processability and mechanical properties at the same time, to achieve the goal beyond tensile strength and conductivity.
Patience to wait for the new aluminium alloy, is belong to automatic network with otsuka institute of technology in flat well macro tree.Hirai delegated responsibility, is for electrical use difficulty of high aluminum, developed with high reliability of terminals.
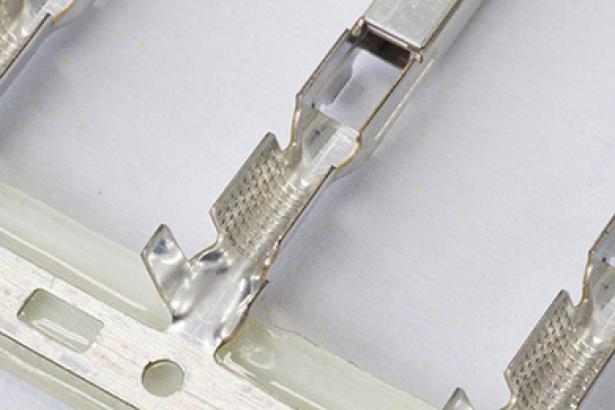
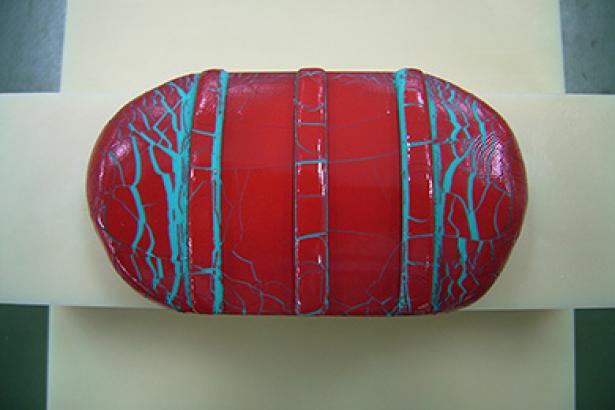
Terminals in the sawtooth is the key
The wiring harness is full of car interior.Some models of wire can be up to about 2000.It is obvious that need to be in the car parts connect wiring harness and wire harness.Connected wire is adopted is known as pressure welding technique, form the wire connecting terminals with insert joint phase chimeric structure.Refers to the pressure to terminal and wire connection method of phase conjugation by physical pressure, to ensure that electrical connections and wires.To further development of aluminium wire bundle, horizontal Wells have mainly focused on based on the way of pressure to the establishment of aluminium wire and terminal connection technology.
"People think the materials properties of aluminum, affect pressure welding.The surface of the aluminum, covered with solid insulation oxide film.Originally is a kind of difficult to achieve material of electrical connections.Therefore, in order to ensure the electrical connection, in the process of pressure welding, the destruction of solid insulation oxide film has become the biggest issue.At this time of the breach is the terminal of the sawtooth "(the horizontal well)
Sawtooth refers to pressure or move terminal wire groove which is formed by the connection parts, the parts after pressure can prevent the wire fall off.People found for aluminium wire, if use serrated destruction of oxide film on the surface of the wire, can significantly improve the stability of the electrical connection in the terminal and wire.Horizontal Wells experiment is extremely unique.The process may be called the aluminum oxide capsule "visualization", the simulation of the oxide film paint on clay, clay modeling wires, reoccupy simulation terminal crushed clay.Results confirm the sawtooth clay appeared near the large deformation, the coating was damaged."On the spot to further exert load, wire and terminal XinShengMian will link together (tin condenses on the aluminum wire), to ensure the electrical connection.In addition to the simulation experiments of clay, we also through CAE analysis, joint state precision analysis and so on more than 60 test and inspection, found that in order to ensure the connection reliability, need to increase the wire and terminal agglutinate place - serrated.Should try to become the focus "of the terminal development of horizontal Wells (above)
In order to improve the electrical connection in the performance of the birth of a new terminal in ensuring at the same time, the amount of serrated in order to improve the wire and stability, also joined the tiny bump a wide scale.More important, only through the change of serrated ensures that connectivity.Through flexible application of previous terminal production assets, able to cut costs sharply.In terms of production, through cooperation with sumitomo denso parts business based connection technology, implements, including welding process to ensure the quality of the sawtooth and pressure connection reliability.Horizontal Wells are pushing terminal development, has become the realization and other companies clearly differentiation factor.
Then, in a series of aluminium wire bundle cannot be avoided in the development, is the aluminum corrosion protection technology development.Relevant controller is peace well belong to automatic network can institute of technology in the wild.
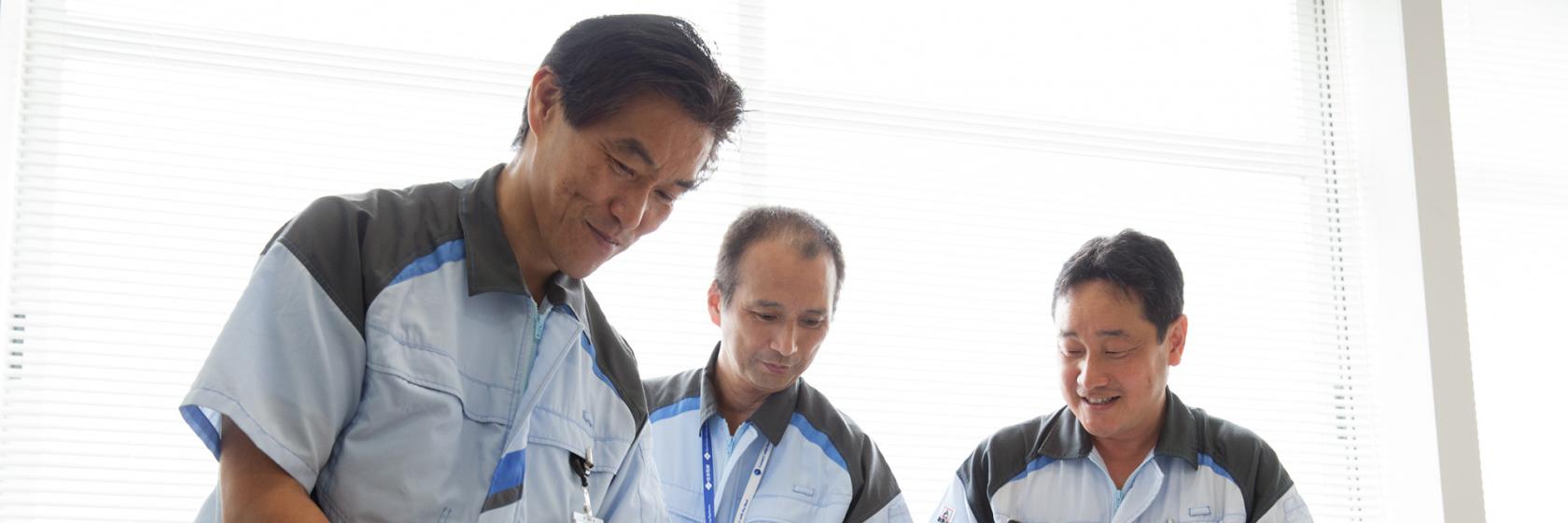