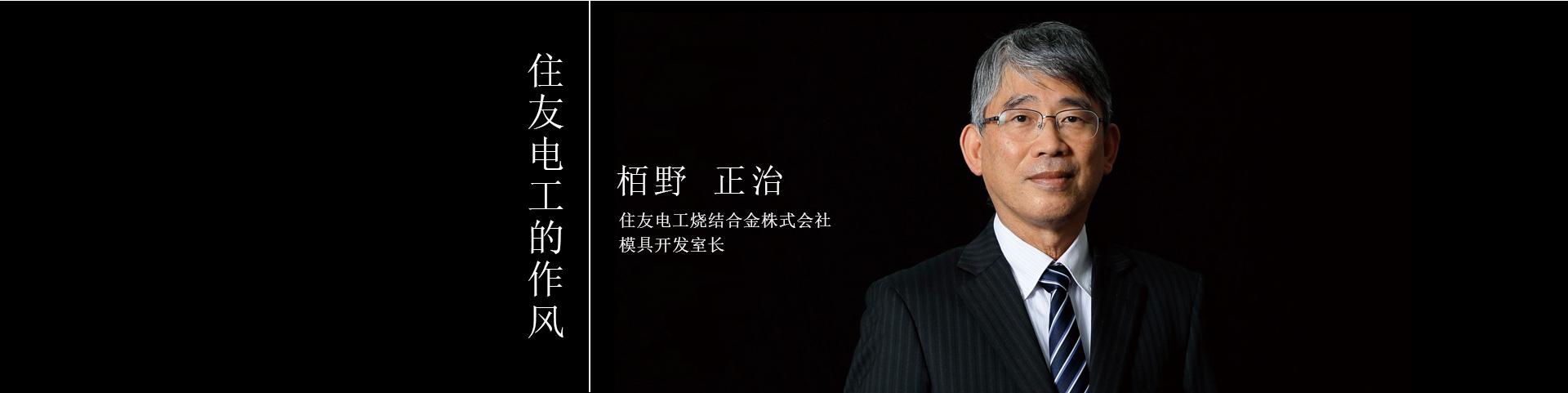
The key to die - sintering parts manufacturing process
Since induction, I has been committed to the mould manufacturing.Mold is to point to: use stamping processing technology to make human life to use when the required precision industrial components metal instruments.Due to the mould quality directly affects the quality of the products and performance, so it is also known as the cornerstone of "manufacturing".I have committed to develop mold is mainly used for manufacturing the company's core products "sintering parts", the products in our company name also.Sintered parts are made by powder metallurgy method ", namely: to give priority to with iron, a variety of fine metal powder compression molding at above 1000 ℃ high temperature sintering.Sintering parts because it has the advantages of high dimensional accuracy, and is widely applied in automobile, agricultural machinery, office equipment and home appliances and other industries.
There have been quite a long time, the company's mold manufacturing is outsourced to other companies.But in my entry in 1984, the company began to try to manufacture of moulds, so soon after the induction, I received the led indicator, became a member of the mold development team, and mould of homemade 1 students.In university majored in welding, however I don't know anything about mould knowledge is.In order to "experience and technology, I Dan sumitomo electric mold department internship in Iraq for about 1 year time, starting in 1985 formally participate in mould manufacturing development.As mentioned earlier, the quality of the mould itself may have a big impact on product, so need to ensure high precision mould manufacturing.And a mold manufacturing takes about a month, once the failure, will seriously affect the product delivery time, bring great economic losses to the company.Then, as a key project in the company, in which there cannot be any wrong tense atmosphere, we start the mould development business.
Challenge makes sense
Mould manufacturing is highly professional field, it is necessary to master the most advanced equipment and technology.I itself is through down-to-earth learning technology improve the professional ability, the accumulation of experience.In this process, there is one thing that impressed me.While in the design phase will give full consideration to the mold elements such as intensity, but when the compression molding powder, or break, crack and defect happened unexpected damage problem.
Initially we are through, for example, "from the lateral shackled by using circular steel mould and the compression prestress in order to enhance strength" of the interference fit method to produce hard alloy material extrusion forming part of the mould, but we can only rely on experience, the results were produced in the die strength is insufficient, broken frequently, caused a huge burden for the factory.To solve this problem, we adopt when fashion in the early stages and complex finite element method (FEM) analysis method and empirical experiments at the same time, developed the most suitable for maximum intensity of drum type interference fit method, greatly extend the die life.Mold technology subject back to as a source of mold design stage to solve, this can be a technological innovation at the time.
In 1993, in 9 years I was elected to okayama prefecture skill evaluations committee member, this is a turning point of my life.Skill evaluations is Japan a judge "work mastering the skills of" national testing system, a total of 130, including processing and building woodworking machinery, such as the kind of career for evaluation.Eligible for examination and assessment can be gained the title of "skill".Among them, prepare the skill evaluations implementation main point, the verification test scores as well as to guide and supervise is the skill evaluations committee is responsible for the work, but I did not initially served as member skill evaluations.At that time, the skill evaluations of career added machining and edm, I hope I can actively challenge employees skills, so they overlap and skill checks.In addition to acquire skills and qualifications will become more confident after this goal, there is another reason: I think the challenge is meaningful.In order to greet the arrival of the test date, the skill evaluations challenger will down-to-earth to constant practice.In accepting the verification, will be more attentively in the machinery.I think to qualified the road of studying hard is very important, because they can improve our technical ability and the level of job, and let a person get a sense of accomplishment.When the internal activity, okayama prefecture government sent to our company "hope recommend skill evaluations committee" invitation letter, I was selected.About 25 years after that, I have served as a skill check members.So far, the company has about 50 people acquire the skills of the title.
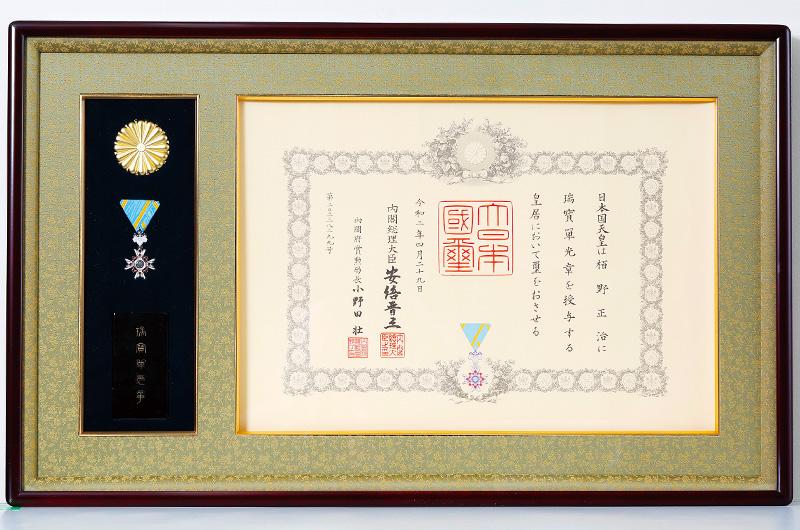
Because of the skill evaluations such as credit and was awarded the "red treasure presented.especially chapter"
Because of the credit for skill evaluations, I has won several awards, but the spring in the decorated by the government awarded the "red treasure presented.especially chapter", let me more than happy.I regarded it as his whip.As a skill check member, although I got "to guide and cultivate new and powder metallurgy industry technology level of ascension", but looking back, it is because many boss and predecessors to give guidance, my colleagues and subordinates give me support, I was able to get today's achievement.In this sense, I am a senior and junior as you including representatives of partners won the medal.
"Tortoise and the hare" story to analogy, using powder metallurgy technology of mould manufacturing is the only "tortoise".In this field, not like "rabbit".Therefore, mould manufacturing technology personnel if not like "tortoise" one step a footprint, tirelessly accumulated technology and experience, the true difficult to succeed."Down-to-earth, tireless", this is my style as a technician, can also be called is a kind of style.I hope young people can listen to my advice, to understand the importance of "down-to-earth, tireless".On the other hand, I was just at the time of induction, mould manufacturing technology in mould manufacturing technology and now there are worlds apart.Ever need human to complete the process, now it can be controlled by the most advanced equipment.Predictably, extensive application using technologies such as artificial intelligence, mechanization and automation will be unstoppable.So I hope the young don't formalized, with free active thinking to carry out the research and development work.In the future, in the propaganda and the charm of mould manufacturing and fun at the same time, I will work to build and maintain the young men and women can perform work environment, as a reward.
The PROFILE
Sheba wild shouji Masaharu Kayano
In 1984,
In the original okayama lives electric precision co., LTD
Fell in love with the new mould development room
In 1991,
The company changed its name to sumitomo electric sintered alloy co., LTD
In 1993,
Okayama vocational skill evaluations committee members elected
In 2004,
Won the okayama prefecture governor certificate (the achievement of professional skill verification)
In 2006,
Won the central professional electrical development association of recognition (the achievement of professional skill verification)
In 2014,
Won the minister of health, labor and welfare recognition (the achievement of professional skill verification)
In 2015,
Long development technicians
In 2016,
Mold development for
In 2020,
Chapter was awarded the red treasure are presented.especially, up to now
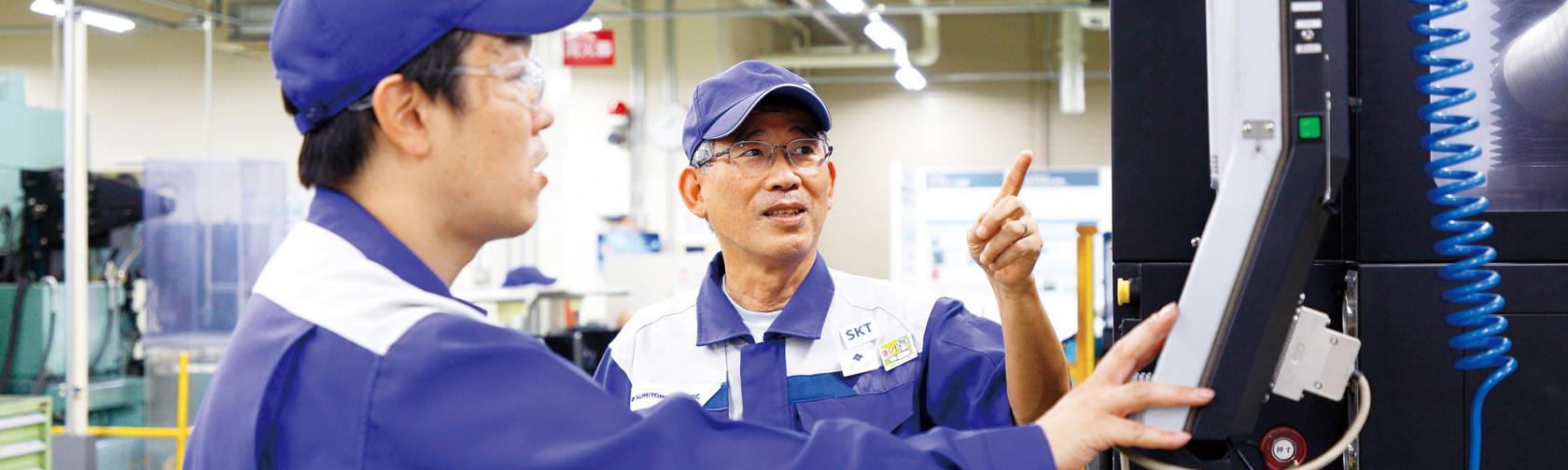